ER630
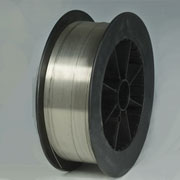
Class: ER630
AWS: A5.9
Conforms to Certification: AWS A5.9 | ASME SFA A5.9
Weld Process Used for Mig: (GMAW) and Submerged Arc (SAW)
AWS Chemical Composition Requirements
C = 0.05 max
Cr = 16.0 – 16.75
Ni = 4.5 – 5.0
Mo = 0.75 max
Mn = 0.25 – 0.75
Si = 0.75 max
P = 0.03 max
S = 0.03 max
Cu = 3.25 – 4.00
Nb + Ta = 0.15 – 0.30
Available Sizes |
|
Diameter X Spool Sizes | Diameter X Coil Sizes |
.025 x 2#, 10#, 25# | 1/16 x 60# & mill coil |
.030 x 2#, 10#, 25#, 30#, 33# | 5/64 x 60# & mill coil |
.035 x 2#, 10#, 25#, 30#, 33# | 3/32 x 60# & mill coil |
.045 x 2#, 10#, 25#, 30#, 33# | 1/8 x 60# & mill coil |
1/16 x 10#, 25#, 30#, 33# | 3/16 x 60# & mill coil |
5/32 x 60# & mill coil |
Application
ER630 classification is designed primarily for welding ASTM A564 type 630 and some other precipitation-hardening stainless steels. The composition is modified to prevent the formation of ferrite networks in the martensitic microstructure which has a great effect on mechanical properties. The weld metal may be used either as welded, welded and precipitation hardened, or welding and solution treated. Mechanical properties of this alloy are greatly influenced by the heat treatment.
Deposited Chemical Composition % (Typical) | ||
C = 0.03 | Mo = 0.20 | P = 0.020 |
Cr = 16.51 | Mn = 0.54 | S = 0.018 |
Ni = 4.75 | Si = 0.41 | Cu = 3.62 |
Nb + Ta = 0.23 |
Mechanical Properties (R.T.) | |
Yield Strength | 150,000psi |
Tensile Strength | 135,000psi |
Elongation | 10% |
Deposited All Weld Metal Properties
They are dependent on the utilization of a post weld heat treatment and a precipitation hardening based on temp, and time exposed to temperature.
Recommended Welding Parameters |
||||||
GMAW “Mig Process” | Reversed Polarity | |||||
Wire Diameter | Wire Feed | Amps | Volts | Shielding Gas | Gas CFH | |
Short Arc Welding | .030 | 13-26 | 40-120 | 16-20 | Argon+2% O2 | 25 |
.035 | 13-26 | 60-140 | 16-22 | Argon+2% O2 | 25 | |
Spray Arc Welding | .035 | 20-39 | 140-220 | 24-29 | Argon+2% O2 | 38 |
.045 | 16-30 | 160-260 | 25-30 | Argon+2% O2 | 38 | |
1/16 | 10-16 | 230-350 | 27-31 | Argon+2% O2 | 38 |
Other shielding Gases may be used for Mig welding. Shielding gases are chosen taking Quality, Cost, and Operability into consideration
Recommended Welding Parameters |
||
SAW “Submerged Arc Welding Process” | Reversed Polarity Suggested | |
Wire Diameter | Amps | Volts |
3/32 | 250-450 | 28-32 |
1/8 | 300-500 | 29-34 |
5/32 | 400-600 | 30-35 |
3/16 | 500-700 | 30-35 |
Both Agglomerated and fused fluxes can be used for submerged arc welding.
Note: The chemical composition of the flux mainly affects the chemistry of the weld metal and consequently its corrosion resistance and Mechanical properties.