Cobalt #12 CTD Electrode
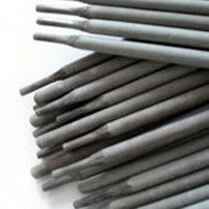
Class: ECoCr-B
AWS: A5.13
DURAMAX COBALT #12 CTD ELECTRODE
Conforms to Certification: AWS A5.13 | ASME SFA 5.13
Weld Process: Shielded Metal Arc
AWS Chemical Composition Requirements | ||
C = 1.0 – 1.7 | Mn = 2.0 max | Si = 2.0 max |
Cr = 25 – 32 | Ni = 3.0 max | Mo = 1.0 max |
Fe = 5.0 max | W = 7.0 – 9.5 | Co = Remainder |
Other = 1.0 max |
Product Description:
DURAMAX Cobalt #12 SMAW electrodes provide excellent hot hardness and abrasion resistance and good corrosion resistance. These properties make DMCobalt#12 well suited for wood cutting saws and bars and for industrial cutting applications for carpet, plastics, paper and chemical industries. This electrode is recommended for metal–to-metal abrasion involving high temperature and/or corrosive media with moderate impact. The weld deposits are smooth and it acquires a high polish in use. This alloy is nonmagnetic and is not forgeable. It can be machined with difficulty using carbide tools. It bonds well to all steels, including stainless.
Typical Applications: |
|||
– Chain Saws Blades | – Chain Saw Bars | ||
– Saw Teeth | – Extrusion Dies | ||
Deposited Chemical Compositon % (Typical) | |||
C = 1.5 | Mn = 0.9 | Si = 1.1 | |
Cr = 28.7 | Ni = 2.6 | Mo = 0.1 | |
Fe = 3.1 | W = 8.5 | Co = Balance | |
Typical Deposit Characteristics: |
|||
– Abrasion Resistance | Excellent | – Hardness | HRC 34 – 47 |
– Impact Resistance | Good | – Hot Weld Hardness | Excellent |
– Corrosion Resistance | Good | – Deposit layers | 2 Layers Max |
– Magnetic | No | – Metal-to-Metal Wear | Excellent |
– Machineability | Difficult use Carbide tools | – Deposit Cross Check | No |
Recommended Operation of Welding Rods
Flat Welding
Diameter | Amps DCEP |
1/8 | 90 – 120 |
5/32 | 145 – 165 |
3/16 | 175 – 195 |